Our Blogs
Dry Type Transformer: Definition, Types, Advantages, and Applications
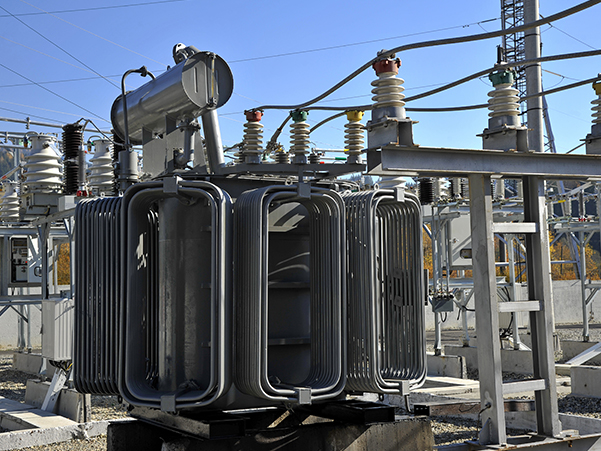
A dry-type transformer is characterized by its exclusion of any liquid substance as an insulator or coolant for its windings and core. Instead, these essential components are enclosed within a sealed tank, typically filled with air or gas under pressure.
The prevalence of dry-type transformers across diverse industries and applications can be attributed to their inherent safety, reliability, and environmental advantages. These transformers demonstrate resilience in challenging environments, including high humidity, fire-prone conditions, and seismic events, all while maintaining optimal performance and ensuring the safety of individuals and property.

Dry Type Transformer
This article delves into a comprehensive exploration of dry-type transformers, covering their various types, merits, drawbacks, applications, and the pivotal considerations entailed in the design process of these transformers.
Types of Dry-Type Transformers
Two primary types of dry-type transformers include: Cast Resin Dry-Type Transformer (CRT) and Vacuum Pressure Impregnated Transformer (VPI).
Cast Resin Dry Type Transformer (CRT)
A cast resin dry-type transformer (CRT) is a transformer variant that utilizes epoxy resin to encapsulate both its primary and secondary windings. This protective encapsulation shields the windings from environmental elements such as moisture, dust, corrosion, and other factors that might compromise their insulation and overall performance.
Noteworthy for its resilience, a CRT is well-suited for deployment in high humidity environments, indoor installations, and areas prone to fire risks. Its non-hygroscopic and non-inflammable nature, coupled with being maintenance-free, makes it a robust choice. The CRT's ability to withstand overloads, partial discharges, and its low losses contribute to high efficiency and an extended service life.
Vacuum Pressure Impregnated Transformer (VPI)
A vacuum pressure impregnated transformer (VPI) is a transformer variant that employs class H polyester resin to impregnate its windings under both vacuum and pressure conditions. This meticulous process eliminates any air gaps or voids within the insulation, leading to improved mechanical strength, dielectric strength, and thermal stability.
Designed for robust performance, a VPI transformer finds suitability in outdoor installations, seismic events, and regions with temperature fluctuations. Its sturdy construction, moisture-resistant enclosure, and low thermal expansion coefficient contribute to its resilience. Noteworthy features of a VPI transformer include easy maintenance, a low risk of fire, and high resistance to short-circuit currents.
VPI transformers are available in a range of ratings, spanning from 5 kVA to 30 MVA, with insulation classes of F (155°C) or H (180°C), and protection levels extending up to IP56.
CRTs are available in a range of ratings, spanning from 25 kVA to 12,500 kVA, with an insulation class of F (allowing for a 90°C temperature rise).
Advantages of Dry Type Transformers
Dry-type transformers offer a multitude of advantages, including:
- Safety: They pose minimal risk to people and property as they lack flammable or toxic liquids that could leak or catch fire.
- Maintenance-Free and Pollution-Free: These transformers require no oil changes, oil tests, spill cleanup, or special disposal methods, contributing to both low maintenance and environmental friendliness.
- Ease of Installation: Installation is straightforward, as dry-type transformers do not demand vaults or special foundations. Placing them near the load minimizes the need for lengthy and expensive low-voltage cables.
- Environmental Friendliness: With no emissions of harmful gases and no contribution to the greenhouse effect, dry-type transformers stand out as environmentally conscious solutions.
- Overload Capacity: They exhibit excellent support for overloads, thanks to superior heat dissipation and thermal endurance compared to oil-filled transformers.
- Reduced Civil Installation Costs: Dry-type transformers eliminate the need for oil containment pits, fire walls, fire extinguishers, or sprinklers, resulting in cost savings on civil installation works and fire protection systems.
- Seismic Resilience: Their rigid structure enables them to withstand vibrations and shocks, ensuring excellent performance during seismic events.
- Fire Hazard Mitigation: Dry-type transformers possess self-extinguishing properties, minimizing the risk of fires. They do not produce smoke or flames in case of faults.
- Resistance to Short-Circuit Currents: These transformers boast low impedance and high mechanical strength, providing excellent resistance to short-circuit currents.
- Longevity: The use of high-quality insulation materials allows dry-type transformers to withstand high temperatures without degradation, ensuring a long-lasting operational life.
- Suitability for Damp and Contaminated Areas: Featuring high moisture ingress protection and corrosion resistance, dry-type transformers are well-suited for operation in damp or contaminated environments.
Disadvantages of Dry Type Transformerss
Dry-type transformers, despite their numerous advantages, come with certain disadvantages:
- Higher Cost: Dry-type transformers tend to be more expensive than oil-filled transformers with the same power and voltage rating. This increased cost is attributed to the need for more materials and labor during the manufacturing process.
- Larger and Heavier: In comparison to oil-filled transformers of equivalent power and voltage ratings, dry-type transformers are larger and heavier. This is due to the presence of additional air gaps and insulation thickness.
- Sensitivity to Environmental Factors: Dry-type transformers are more susceptible to dust, dirt, and vermin. Their open ventilation design allows the entry of foreign particles, potentially causing damage to the windings or leading to short circuits.
- Noise Levels: Dry-type transformers generate more noise compared to their oil-filled counterparts. This heightened noise is a result of increased magnetostriction and vibration, contributing to audible sounds during operation.
Applications of Dry Type Transformers
In particular, traction TFs are employed to convert the power produced by the traction effect when trains are moving. The electric motors receive this energy after that.
Dry-type transformers find widespread use across diverse industries and applications, owing to their emphasis on safety, reliability, and environmental compatibility. Here are some common applications:
- Chemical, Oil, and Gas Industry: Dry-type transformers supply power to equipment and processes in environments with flammable or explosive substances, such as refineries, petrochemical plants, pipelines, and offshore platforms.
- Environmentally Sensitive Areas: Utilized to safeguard the environment in locations where oil spills or leaks could contaminate water sources, soil, or wildlife habitats. Examples include water protection areas, forests, and wetlands.
- Fire-Risk Areas: Deployed to prevent fire hazards or minimize damage in areas prone to fire outbreaks or subject to stringent fire regulations. This includes indoor substations, underground substations, hospitals, schools, hotels, and shopping malls.
- Renewable Generation: Dry-type transformers facilitate the connection of renewable energy sources, such as wind turbines, solar panels, and hydroelectric plants, to the grid or directly to the load.
- Other Applications: Used in various applications requiring high performance, low maintenance, or special features, including:
- Traction Systems: In transportation systems, such as trains.
- Marine Systems: For powering equipment on ships and offshore platforms.
- Mining Systems: Providing power in mining operations.
- Data Centers: Ensuring reliable power distribution in data center facilities.
The versatility and reliability of dry-type transformers make them suitable for a broad spectrum of industries and applications where safety, environmental considerations, and robust performance are paramount.
What are the Important Factors to Design a Dry Type Transformer?
The design of a dry-type transformer involves careful consideration of several key factors that significantly impact its performance, efficiency, and durability. Here are important aspects to take into account during the design process:
- Choice of Insulation Type: The insulation type, such as F or H-class materials like varnish, epoxy resin, or polyester resin, dictates temperature rating, dielectric strength, mechanical strength, and thermal shock resistance. These materials are selected for their ability to withstand high temperatures (up to 155°C and 180°C) and exhibit favorable electrical and mechanical properties.
- Selection of Winding Material: Copper and aluminum are commonly used as winding materials due to their high conductivity and cost-effectiveness. Copper offers superior conductivity and mechanical strength but is heavier and more expensive than aluminum. The choice depends on factors like cost, weight considerations, and specific application requirements.
- Core Material with Low Hysteresis Loss: The core material, such as silicon steel, cold-rolled grain-oriented steel (CRGO), or amorphous metal, influences magnetic flux density, permeability, hysteresis loss, and eddy current loss. Optimal core material selection is crucial for reducing no-load losses and enhancing transformer efficiency.
- Regulation: Regulation is the ratio of voltage drop at full load to no-load voltage, indicating the transformer's ability to maintain a constant output voltage under varying load conditions. Low impedance and resistance contribute to low regulation, enhancing voltage regulation. Keeping leakage reactance within 2% during design helps achieve low regulation.
- Life Expectancy: The expected operational lifespan depends on insulation breakdown due to factors like temperature rise, moisture, dust, and corrosion. Choosing an appropriate insulation class and quality is vital for durability, and the transformer's temperature rise should not exceed the specified limit for the insulation class.
- Losses: Transformers incur losses, including no-load losses (core loss and eddy current loss) and load losses (copper loss and stray loss). Minimizing losses through careful selection of core, winding, and insulation materials, as well as design parameters, maximizes efficiency and influences heating and cooling characteristics.
- Overloading: Designing transformers with sufficient margins to handle overloads without damage is critical. Overloading can result from excessive load demand, harmonics, faults, or ambient temperature variations. Incorporating fan-cooling or air-conditioning systems aids in dissipating heat generated during overloads.
- K-Factor: K-factor measures a transformer's ability to withstand heat generated by non-sinusoidal currents. High K-factor transformers are designed to handle higher levels of harmonics generated by electronic devices, ensuring longevity and reliable performance in applications involving non-sinusoidal currents.
Conclusion
A dry-type transformer relies on air or gas for insulation and cooling, utilizing epoxy or polyester resin. The two main types are cast resin (CRT) and vacuum pressure-impregnated (VPI), each with distinct pros and cons based on application and environment.
Benefits of dry-type transformers include safety, reliability, environmental compatibility, easy installation, low maintenance, overload capacity, cost reduction, excellent performance, no fire hazard, resistance, long life, and suitability for damp areas. Nevertheless, they come with drawbacks such as higher cost, larger size, increased weight, sensitivity, and higher noise compared to oil-filled transformers.
Design considerations for dry-type transformers involve insulation type, winding and core material selection, regulation, life expectancy, losses, overloading capacity, K-factor, and insulation level.
Widely used in industries requiring safety and reliability, common applications include the chemical, oil, and gas sector; environmentally sensitive areas; fire-prone zones; renewable energy generation; and diverse applications across different industries.